Written by Stuart Hood and Thomas Bamber from the Integral Group
The mechanical system at the Radcliffe Passive House was designed to achieve year-round comfort from minimal energy consumption. We wanted a highly efficient HVAC solution that achieves simplicity through a limited number of components.
Prior to selecting systems we needed loads for each space. From conception the house had been designed according to Passive House principles that minimize the thermal energy demand. PHPP modelling had calculated a peak heating load of 2.8kW and peak cooling of 2.5kW for the whole house. Our mechanical consultants Integral Group undertook an alternate analysis using an hourly thermal modelling software, EDSL Tas.
Given the large amount of glass on the south face of the home our one concern was overheating. We wanted to test whether supplementary cooling would benefit the heavily glazed Living Area and Master Bedroom at the top of the house. We modelled the house under a Vancouver and an Abbotsford weather file with higher temperatures, to be conservative and allow for an increase in temperatures due to climate change.
The thermal model showed that despite the shading from the overhangs, solar gains were an issue. Reducing the solar heat gain coefficient (SHGC) of the glazing from the design value of 0.69 to 0.42 cut peak cooling in the Master Bedroom from 2.5kW to 1.7kW for the scenario of an Abbotsford summer with thermostat set to 25degrees (in line with PHPP). Even with improved glazing, the total cooling load for the house was calculated at 4.4kW; roughly double the PHPP model.
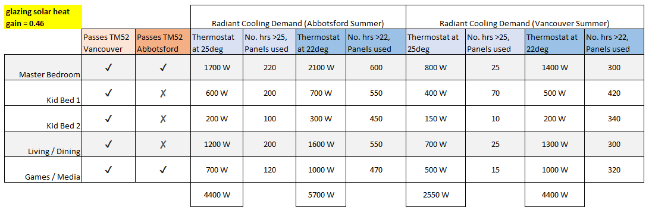
The simulations also demonstrated that the operable windows and sliding doors situated throughout the house can create generous airflows in summer. The free cooling generated from natural ventilation can be used either as a mixed mode system with mechanical ventilation or even as a stand-alone solution for preventing overheating. We tested the performance of natural ventilation without mechanical cooling and found that many of the spaces passed the overheating criterion CIBSE TM52 – an established benchmark for summertime comfort in naturally ventilated buildings.
On the basis of the thermal analysis, we improved the SHGC of the whole house and provided top-up cooling to the Master Bed only using a Jaga fan-coil. All spaces would have cooling via the mechanical ventilation system and the option to boost airflow by opening windows.
For the heat recovery ventilation system we specified a Zehnder Energy Recovery Ventilator (ERV) with an 89% thermal efficiency plus latent recovery. One unit supplies and exhausts from the whole house, including washrooms. Instead of ductwork we used a prefabricated Comfotube duct system, which integrates cleanly with the architectural design. Spaces requiring greater airflow are provided with additional 3″ plastic Comfotubes. In keeping with the mantra of heat recovery, we are installing drain water heat recovery using a PowerPipe which recovers heat otherwise lost from the bath and shower drain water and transfer it into the incoming cold water make up to the hot water tank and shower mixing valve cold water pipe.
It was calculated that we could deliver both our peak heating and cooling using a 2-ton Daikin Altherma air to water heat pump. The Altherma also provides domestic water heating, with a top-up immersion heater. The heat pump can switch between heating and cooling, so in summer the hot water tank is kept full, while the house is cooled. To deliver heat and cool air around the house, we took advantage of the ventilation system by installing 2 coils in the Zehnder ERV supply air discharge to allow for two separate zones in the house.
What makes this so simple and efficient is the absence of pipework and terminal units. Heat is pumped to the ERV Comfocoil and to one additional Jaga unit coil in the Master Bedroom. To make this strategy work, the ventilation air (and hence heat supply) had to be carefully balanced around the house. When peak summer and winter conditions occur, the unit can step into ‘boost mode’, increasing the heating or cooling output through greater air supply. There is also local heating top-up provided by towel radiators, Nu-heat electric floor heat in the bathrooms and a wood burning sealed combustion high efficiency fireplace in the Living Area from Stuv.
We used Tekmar Controls to bring everything (even the towel rails) onto a centralized panel and allow remote control and monitoring from a smart phone or tablet.
With this simple mechanical design and taking advantage of the excellent building envelope, triple glazed glass and over hangs of the Passive House we are able to eliminate the cost and complexity of traditional heating and cooling systems like ducted force air, VRF or in-floor radiant.
This design of the mechanical system in the Westbay Passive House will bring excellent comfort, energy efficiency, lower cost and healthy indoor air for the Dean family.